Процесс производства изделия на термопластавтомате
Изготовление изделий из полимерных материалов
“
А вы знали, что более трети штучных изделий из полимерных материалов изготавливается именно с помощью термопластавтомата? Давайте подробнее разберемся в том, как он работает.
Глоссарий
Для успешного освоения материала рекомендуем вам изучить следующие понятия:
Изотермический процесс
Термодинамический процесс, происходящий в физической системе при постоянной температуре
Гомогенная система
Однородная система, химический состав и физические свойства которой во всех частях одинаковы или меняются непрерывно
Шнек
Стержень со сплошной винтовой поверхностью вдоль продольной оси
Сопло
Канал переменного или постоянного поперечного сечения круглой, прямоугольной или иной формы, предназначенный для подачи жидкостей или газов с определенной скоростью и в требуемом направлении
Пластикация
Процесс превращения твердых пластиковых гранул в расплав
Литник
Отверстие или трубка, через которую в литьевую форму вливается впрыскивается расплав
Коробление
Дефект отливки в виде отклонения от первоначального размера, формы или контура
Видеолекция
Конспект
Литье под давлением
Процесс литья под давлением можно разбить на следующие стадии:
1. Дозирование материала и загрузка в цилиндр, сушка и поступление материала в загрузочный бункер литьевой машины.
1. Дозирование материала и загрузка в цилиндр, сушка и поступление материала в загрузочный бункер литьевой машины.
2. Пластикация материала: транспортирование гранул вращающимся шнеком в нагревательном цилиндре, пластикация и гомогенизация в межвитковом пространстве.
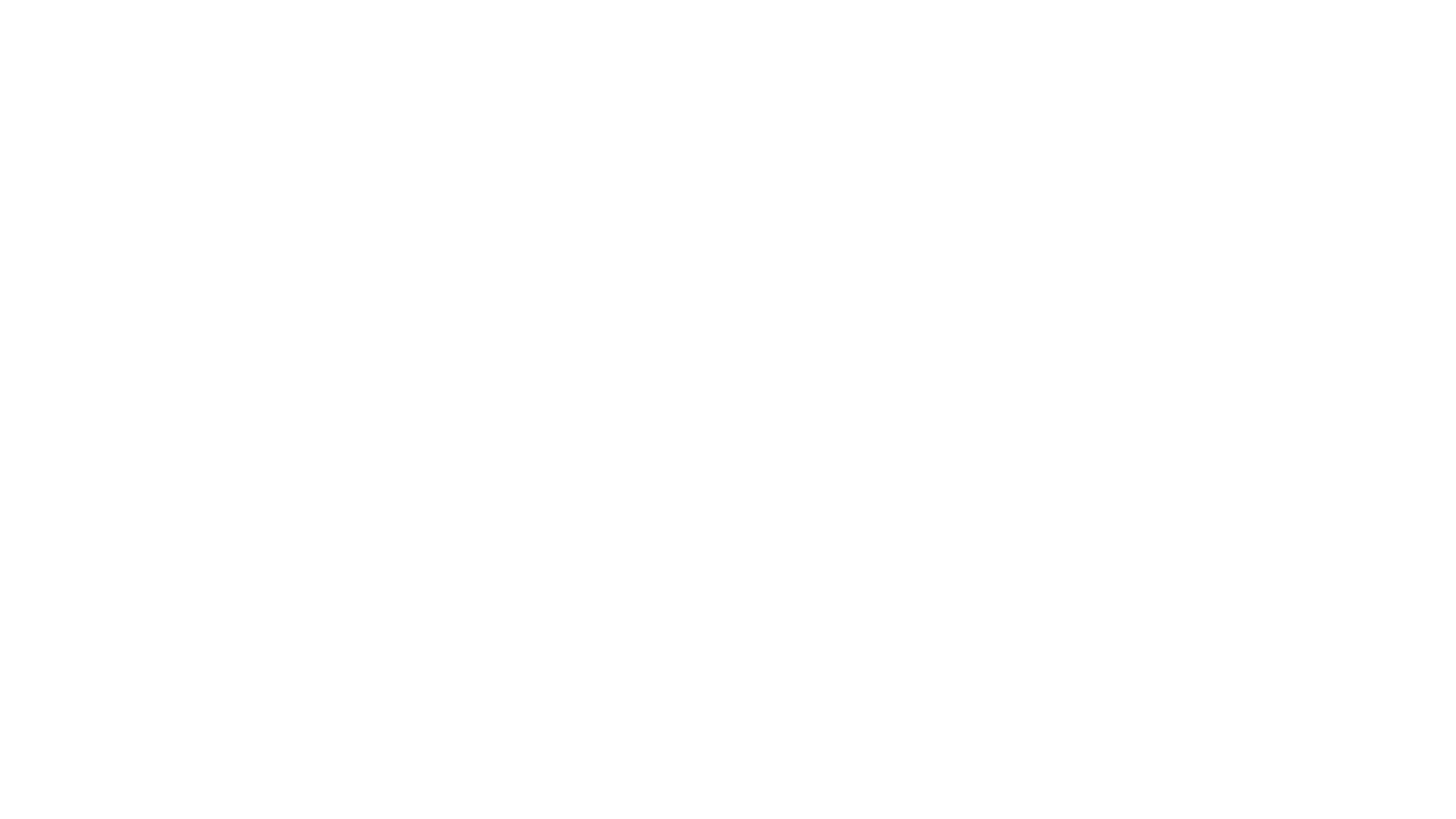
3. Впрыск пластифицированного материала в сомкнутую форму и выдержка его под давлением: сжатие расплава в предмундштуковой зоне до 800−2500 бар, впрыск расплава через мундштук и литник в холодную литьевую форму и заполнение формы, сопровождаемое изотермическим течением расплава полимера в условиях высоких скоростей сдвига.
4. Охлаждение изделия в форме, интенсивная теплоотдача от полимера к форме с застыванием полимера, окончательное затвердевание отливки с возрастанием плотности, уменьшением объема, увеличением литьевой усадки и формированием структуры.
5. Размыкание формы и удаление изделия из нее, постлитьевое охлаждение отливки после выталкивания из формы, сопровождаемое дополнительной усадкой и короблением.
5. Размыкание формы и удаление изделия из нее, постлитьевое охлаждение отливки после выталкивания из формы, сопровождаемое дополнительной усадкой и короблением.
Параметры литьевого цикла
Параметры литьевого цикла можно разделить на следующие стадии:
1. Смыкание формы.
1. Смыкание формы.
Цель — организовать максимально быстрое и деликатное смыкание формы с требуемым усилием запирания и обеспечить ее удержание во время впрыска, выдержки и охлаждения.
При смыкании формы следует избегать удара, поэтому в конце смыкания скорость замедляют.
2. Подвод сопла с прижиманием мундштука к литниковой втулке.
При смыкании формы следует избегать удара, поэтому в конце смыкания скорость замедляют.
2. Подвод сопла с прижиманием мундштука к литниковой втулке.
Цель — обеспечить максимально быстрый подвод сопла, герметичность в течение впрыска и выдержки под давлением.
3. Впрыск.
Цель — обеспечить заполнение полости формы без переливов и недоливов.
Впрыск, в свою очередь, делится на следующие этапы:
4. Выдержка под давлением.
Цель — обеспечить необходимую для компенсации усадочных явлений в полимере дополнительную подпитку отливки расплавом (по незастывшей сердцевине изделия) до момента перемерзания литниковой системы или элементов изделия.
5. Охлаждение.
3. Впрыск.
Цель — обеспечить заполнение полости формы без переливов и недоливов.
Впрыск, в свою очередь, делится на следующие этапы:
- Заполнение формы.
Заполнение происходит с вытеснением воздуха из формы через вентиляционную систему.
- Сжатие расплава.
Сжатие происходит по завершении полного заполнения формы, при этом давление формы возрастает до максимального.
4. Выдержка под давлением.
Цель — обеспечить необходимую для компенсации усадочных явлений в полимере дополнительную подпитку отливки расплавом (по незастывшей сердцевине изделия) до момента перемерзания литниковой системы или элементов изделия.
5. Охлаждение.
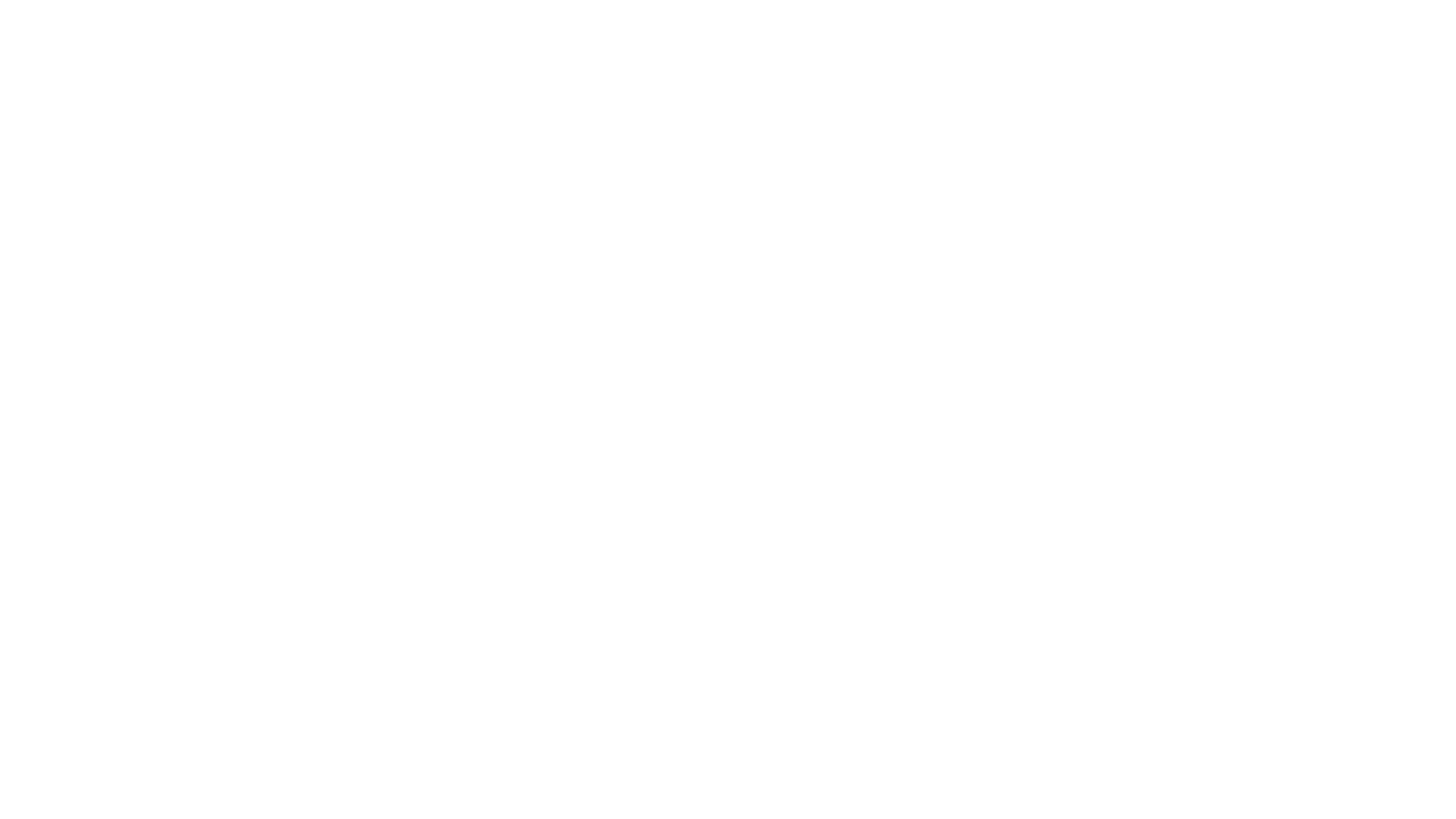
Цель — обеспечить охлаждение полимерной отливки до состояния, при котором может быть осуществлен сброс изделия без необратимых деформаций, коробления и усадки.
По мере охлаждения давление внутри формы постепенно снижается.
6. Дозирование материала.
По мере охлаждения давление внутри формы постепенно снижается.
6. Дозирование материала.
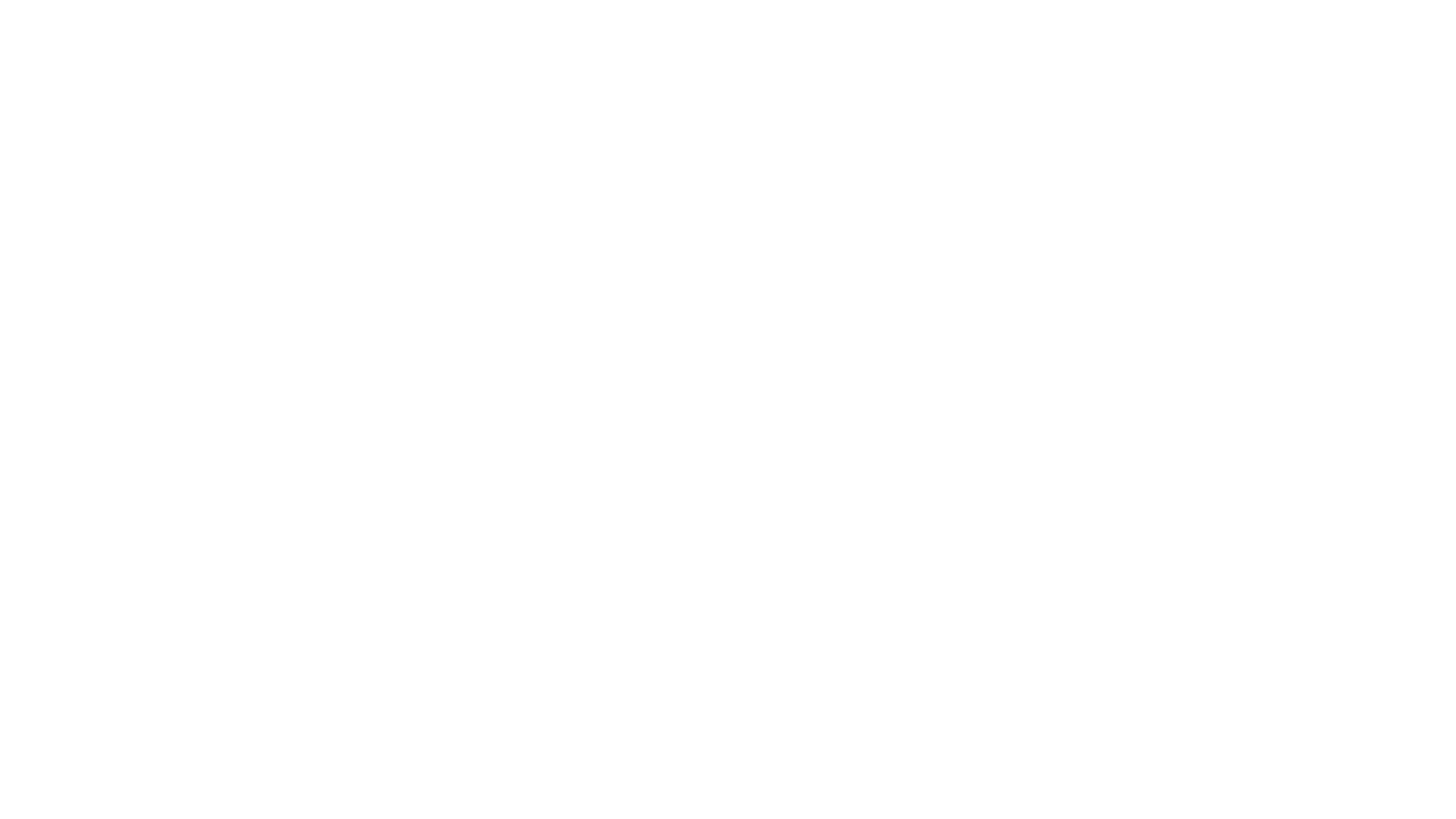
Цель — набор дозы полимерного материала для последующего цикла, чтобы обеспечить высокую концентрационную и температурную гомогенность расплава.
7. Декомпрессия.
Цель — перемещение шнека назад на небольшое расстояние к загрузочной зоне для уменьшения давления в предмундштуковой зоне.
Это необходимое действие при использовании сопла открытого типа, чтобы исключить самопроизвольное истечение предварительно уплотненного расплава после отведения мундштука от формы.
8. Отвод сопла.
Цель — обеспечить отвод сопла, чтобы прервать контакт между литниковой втулкой и соплом. Предотвращает охлаждение сопла или перегрев литниковой втулки во время продолжительного контакта.
9. Размыкание формы.
7. Декомпрессия.
Цель — перемещение шнека назад на небольшое расстояние к загрузочной зоне для уменьшения давления в предмундштуковой зоне.
Это необходимое действие при использовании сопла открытого типа, чтобы исключить самопроизвольное истечение предварительно уплотненного расплава после отведения мундштука от формы.
8. Отвод сопла.
Цель — обеспечить отвод сопла, чтобы прервать контакт между литниковой втулкой и соплом. Предотвращает охлаждение сопла или перегрев литниковой втулки во время продолжительного контакта.
9. Размыкание формы.
Цель — обеспечить быстрое размыкание формы на расстоянии, достаточном для беспрепятственного сброса изделия с учетом особенностей конструкции формы и изделия.
10. Работа системы выталкивания.
10. Работа системы выталкивания.
Цель — обеспечить максимально быстрый сброс изделия за счет перемещения системы сталкивания, а также максимально быстрый возврат в исходное состояние.
11. Температурный режим цилиндра.
Цель — организовать тепловой режим цилиндра для обеспечения смежного плавления полимерного материала.
11. Температурный режим цилиндра.
Цель — организовать тепловой режим цилиндра для обеспечения смежного плавления полимерного материала.
Процесс пластификации материала
Важный рабочий орган узла впрыска — это шнек. Сейчас литьевые машины оснащаются стандартным трехзонным шнеком, который включает в себя:
Процесс пластификации материала происходит следующим образом:
1. Поступающие из бункера гранулы заполняют межвитковое пространство шнека зоны 1 по мере продвижения материала вдоль цилиндра в зоне у загрузочного отверстия. Часть канала заполнена гранулами в области, толкающей поверхности гребня (рис. а). В пассивной части находится воздушная область. Воздух находится в промежутках между гранулами.
2. Через 5−6 витков, к середине загрузочной зоны, в области, толкающей поверхности гребня, начинают накапливаться первые порции расплава, срезаемые гребнем с поверхности цилиндра (рис. б).
3. У пассивной стенки гребня скапливается пробка из непроплавленных гранул. По мере продвижения к концу загрузочный зоны (рис. в) область с расплавом значительно увеличивается и гранулы остаются в компактном виде в небольшой зоне. По мере уменьшения доли гранул уменьшается и количество воздуха между ними.
4. В зоне сжатия толщина канала постепенно уменьшается в 2−2,5 раза, расплав сжимается, еще больше нагревается, занимая все сечение (рис. г). Наблюдается интенсивная циркуляция расплава с остатками непроплавленных гранул.
5. В зоне дозирования (рис. д) устанавливается окончательная температура расплава, при циркуляции в тонком канале он гомогенизируется и через открытый канал поступает в предмундштуковую зону.
- зону загрузки, ее длина составляет 50% от общей,
- зону сжатия, ее длина составляет 25% от общей,
- зону дозирования, ее длина составляет 25% от общей.
Процесс пластификации материала происходит следующим образом:
1. Поступающие из бункера гранулы заполняют межвитковое пространство шнека зоны 1 по мере продвижения материала вдоль цилиндра в зоне у загрузочного отверстия. Часть канала заполнена гранулами в области, толкающей поверхности гребня (рис. а). В пассивной части находится воздушная область. Воздух находится в промежутках между гранулами.
2. Через 5−6 витков, к середине загрузочной зоны, в области, толкающей поверхности гребня, начинают накапливаться первые порции расплава, срезаемые гребнем с поверхности цилиндра (рис. б).
3. У пассивной стенки гребня скапливается пробка из непроплавленных гранул. По мере продвижения к концу загрузочный зоны (рис. в) область с расплавом значительно увеличивается и гранулы остаются в компактном виде в небольшой зоне. По мере уменьшения доли гранул уменьшается и количество воздуха между ними.
4. В зоне сжатия толщина канала постепенно уменьшается в 2−2,5 раза, расплав сжимается, еще больше нагревается, занимая все сечение (рис. г). Наблюдается интенсивная циркуляция расплава с остатками непроплавленных гранул.
5. В зоне дозирования (рис. д) устанавливается окончательная температура расплава, при циркуляции в тонком канале он гомогенизируется и через открытый канал поступает в предмундштуковую зону.
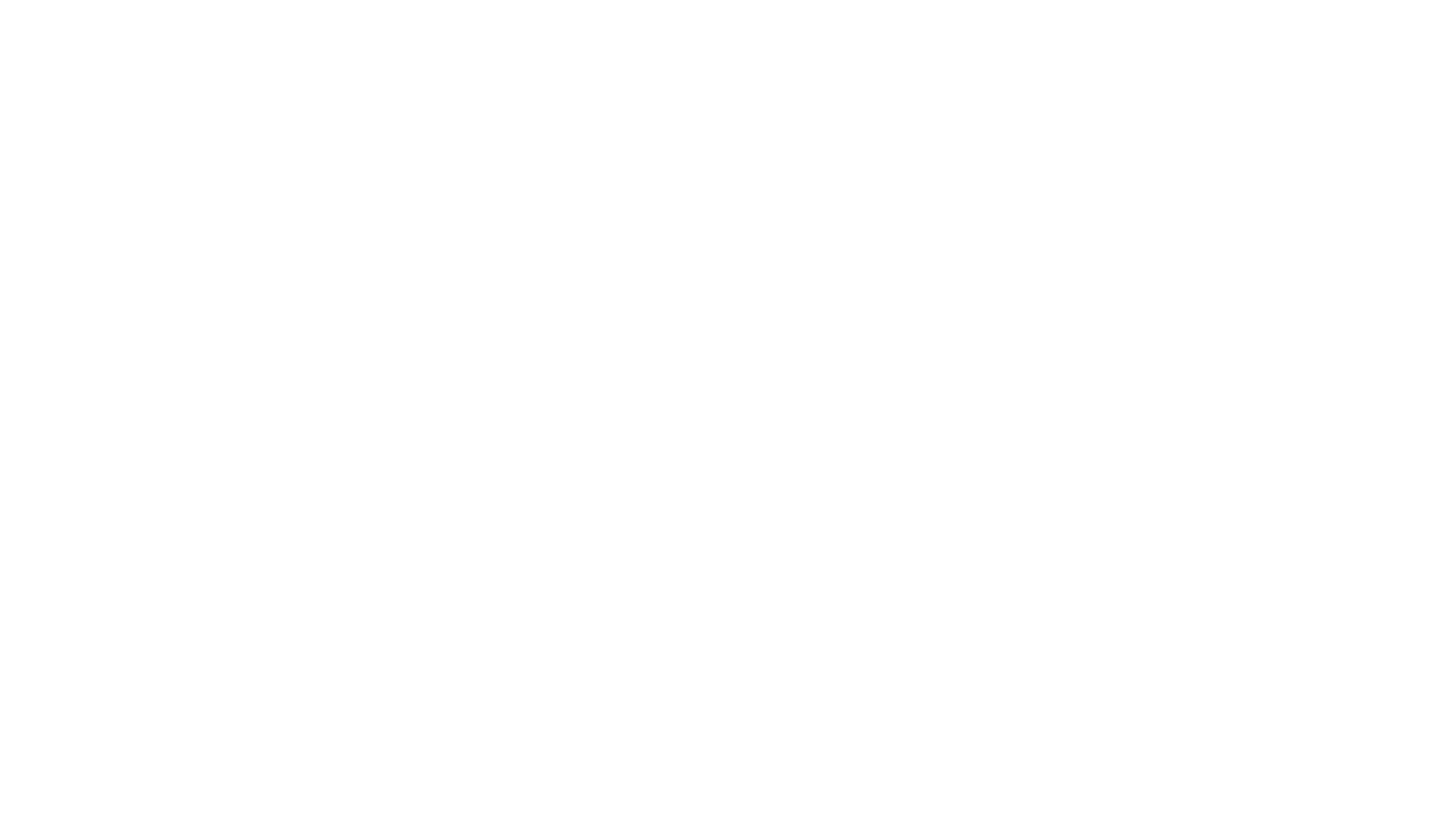
“
На этом все! Теперь вы знаете, каким способом производятся изделия на термопластавтомате. Попробуем закрепить полученные знания на практике?
Интерактивное задание
Тест
Для закрепления полученных знаний пройдите тест
Стартуем! |
Полимерный материал в загрузочном бункере термопластавтомата находится в виде…
Дальше |
Проверить |
Узнать результат |
При застывании объем полимерного материала…
Дальше |
Проверить |
Узнать результат |
Полимерный материал попадает в форму методом...
Дальше |
Проверить |
Узнать результат |
К сожалению, вы ответили неправильно на все вопросы
Прочитайте лекцию и посмотрите видео еще раз
Пройти еще раз |
К сожалению, вы ответили неправильно на большинство вопросов
Прочитайте лекцию и посмотрите видео еще раз
Пройти еще раз |
Неплохо!
Но можно лучше. Прочитайте лекцию и посмотрите видео еще раз
Пройти еще раз |
Отлично!
Вы отлично справились. Теперь можете ознакомиться с другими компетенциями
Пройти еще раз |