Изготовление детали. Чистовая обработка сплава Д16Т. Коррекция размеров
Фрезерные работы на станках с ЧПУ
“
В этом уроке мы продолжим обрабатывать деталь, а именно перейдем к чистовой обработке стенок. Вы научитесь корректировать режимы резания в программе со стойки ЧПУ.
Глоссарий
Для успешного освоения материала рекомендуем вам изучить следующие понятия:
Потенциометр
Рукоять, позволяющая задавать процентное соотношение величины ускоренного хода или рабочей подачи
Скорость резания
Длина пути, пройденного режущей кромкой инструмента относительно обрабатываемой поверхности заготовки за единицу времени, измеряемая в м/мин
Computer-aided manufacturing (CAM)
Автоматизированная система либо модуль автоматизированной системы, предназначенные для подготовки управляющих программ для станков с ЧПУ. Под термином понимаются как сам процесс компьютеризированной подготовки производства, так и программно-вычислительные комплексы, используемые инженерами-технологами
Видеолекция
Конспект
Начнем с запуска программы в автоматическом режиме.
Запуск программы
1. Выберем программу FREZEROVKA_1USTANOV_FINISH. Она заранее была скопирована на локальный диск ЧПУ.
2. Откроем область управления, раздел «Локальный диск». В папке WSR находится искомая программа.
3. Мы не будем редактировать программу, поэтому, не открывая, запускаем ее в автоматическом режиме.
2. Откроем область управления, раздел «Локальный диск». В папке WSR находится искомая программа.
3. Мы не будем редактировать программу, поэтому, не открывая, запускаем ее в автоматическом режиме.
Важно
Для запуска в автоматическом режиме без редактирования надо нажать кнопку «Выполнить», находящуюся в вертикальном ряду многофункциональных клавиш
4. Переходим в область управления и выбираем режим «Авто».
5. Нажимаем кнопку «Пуск» и наблюдаем за выполнением программы.
5. Нажимаем кнопку «Пуск» и наблюдаем за выполнением программы.
Контроль выполнения
- Для контроля в процессе наладки стоит использовать потенциометры, отвечающие за скорость рабочей подачи и ускоренный ход.
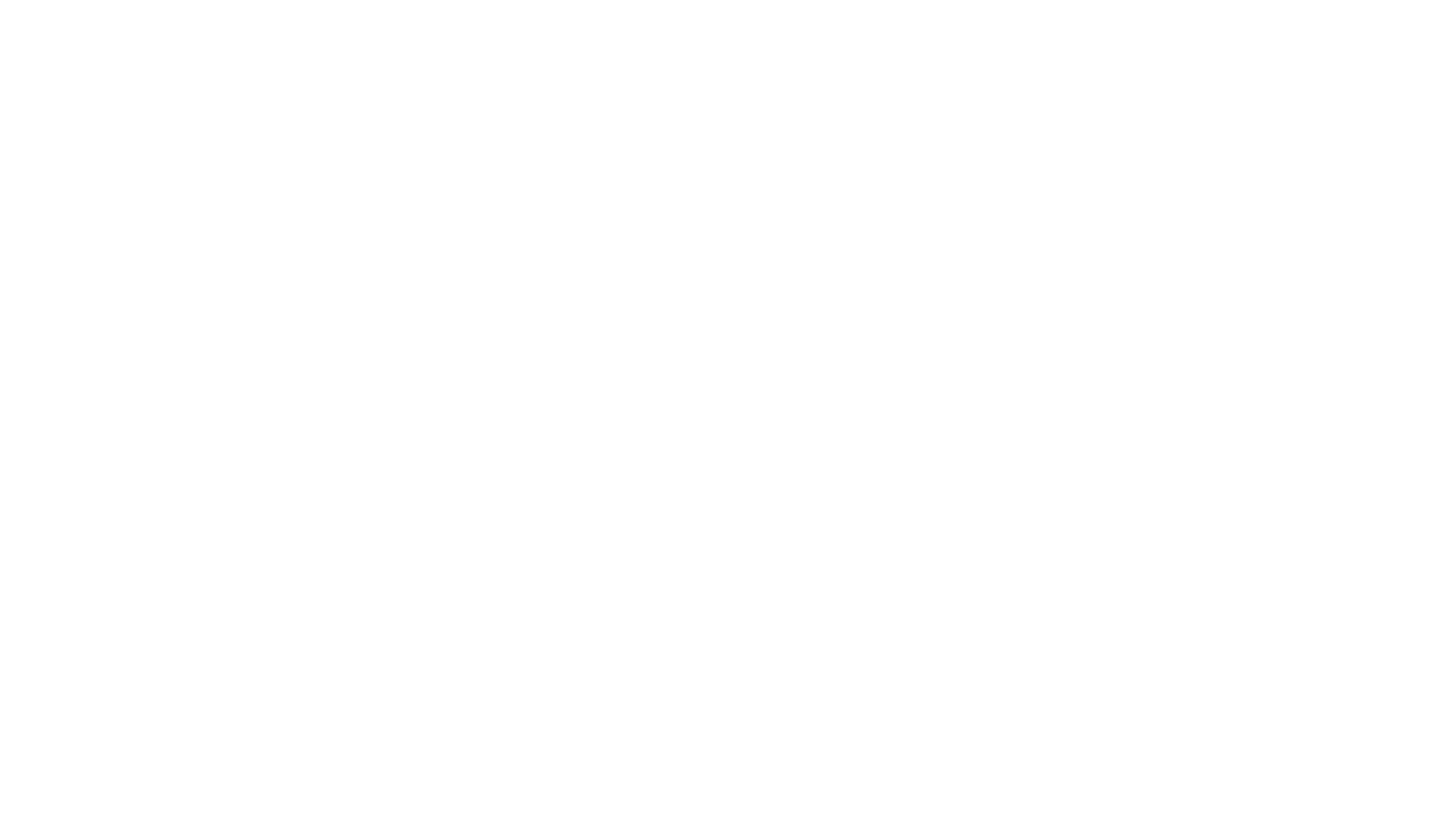
- На клавиатуре присутствуют кнопки, позволяющие менять заданную частоту вращения.
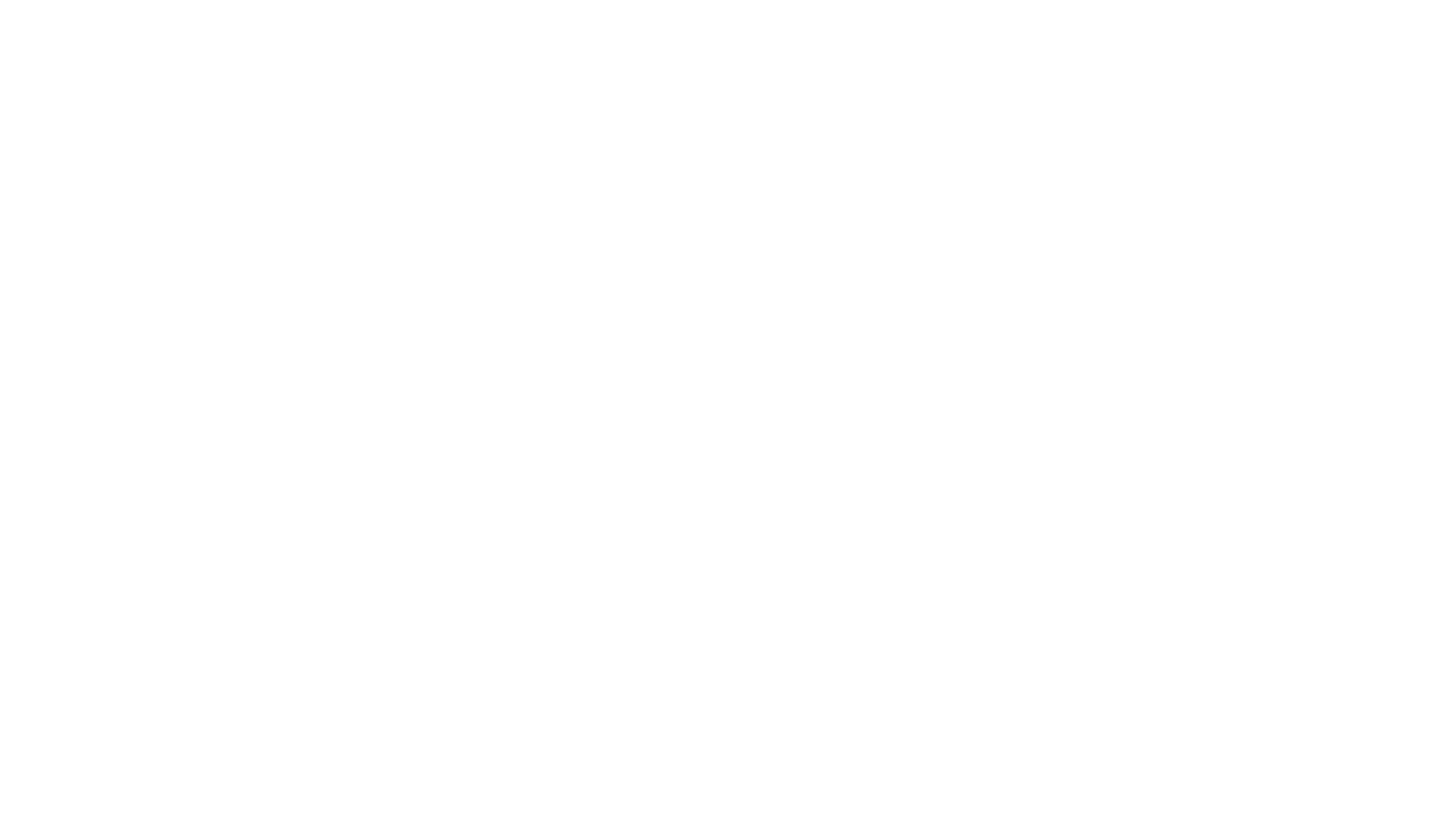
- На дисплее отображаются текущее положение инструмента в выбранной системе координат заготовки и путь, остающийся до завершения перемещения в текущем кадре.
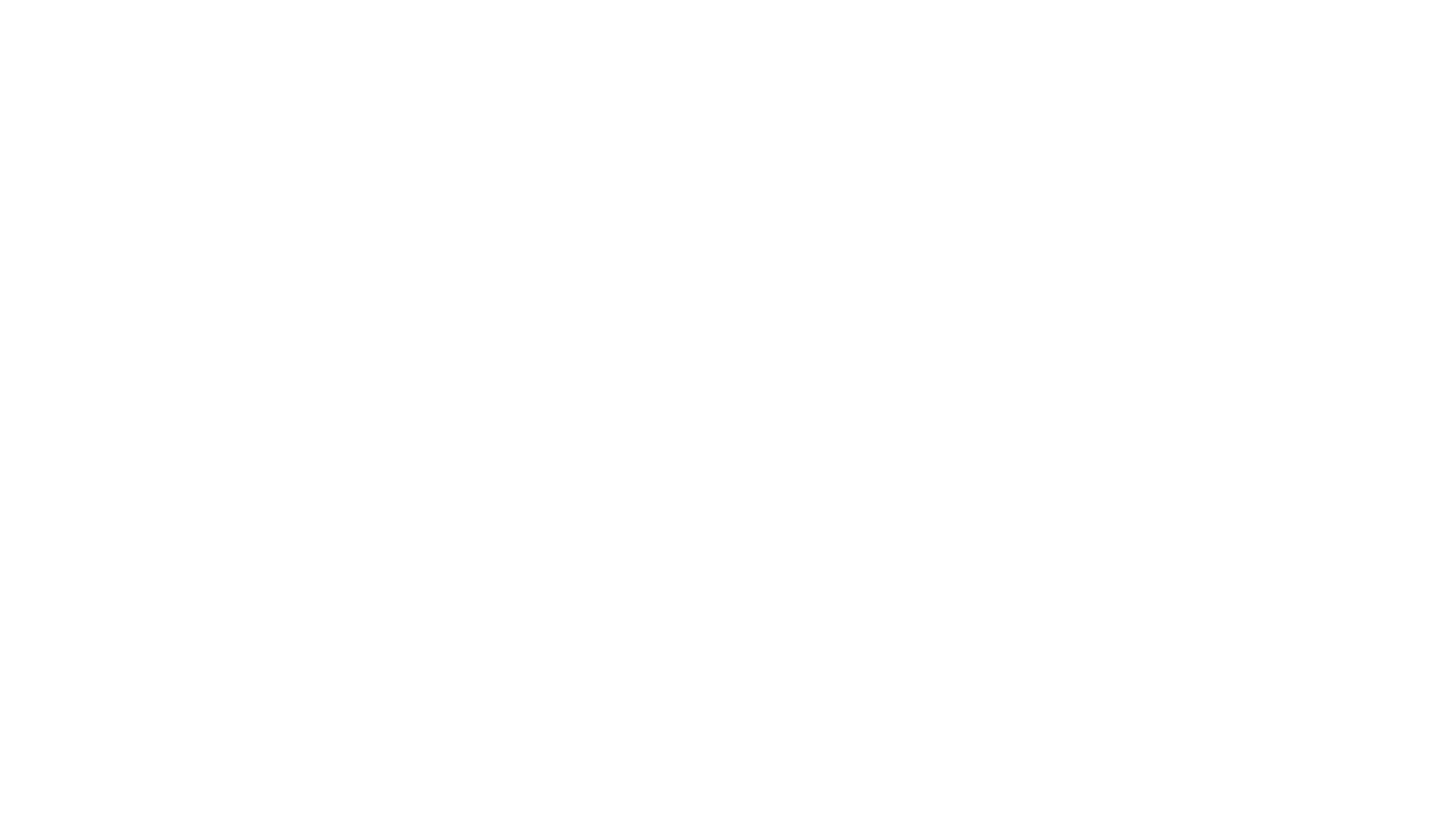
Все это позволяет избежать нежелательных столкновений при наличии ошибок в программе или технологии. Кроме того, при помощи этого инструментария легко подобрать оптимальные режимы резания для конкретных условий обработки.
Факторы процесса резания
При создании технологии и программировании специалист пытается учесть факторы, влияющие на процесс резания:
- скорость резания,
- подача и глубина резания,
- вылет инструмента из оправки,
- тип оправки,
- обрабатываемый материал,
- усилие фиксации,
- концентрация и состав СОЖ.
Важно
Во время наладки на дисплее отображаются не только положение инструмента в системе координат и путь, оставшийся до завершения кадра, но и тип перемещения. Удобно левую руку держать на одном из потенциометров, а правую — рядом с кнопками «Пуск» и «Стоп». При необходимости правой руке достаточно нажать кнопку «Стоп». Левая рука меняет скорость рабочей подачи для подбора оптимальной. В момент, когда вы управляете одним потенциометром, целесообразно второй поставить на значение «0», чтобы дальнейшее переключение между типами перемещений не было для вас неожиданным
Обработка и корректировка
Обработка
Измерения. Фреза 16
После выполнения чистовой обработки необходимо провести измерения выполненных элементов.
- В программе для обработки стенок будем использовать концевые трехзубые фрезы диаметром 6 и 16 мм.
- Контурная обработка снимает припуск, оставленный после черновой обработки, — 0,1 мм на сторону.
Измерения. Фреза 16
После выполнения чистовой обработки необходимо провести измерения выполненных элементов.
- Для измерения охватываемых размеров будем использовать микрометры различных диапазонов.
- Измерим несколько размеров: 76 +/− 0,03; 60 + 0,02 и 60 − 0,02; 55 + 0,05 и 55 + 0,03; 47 + 0,025.
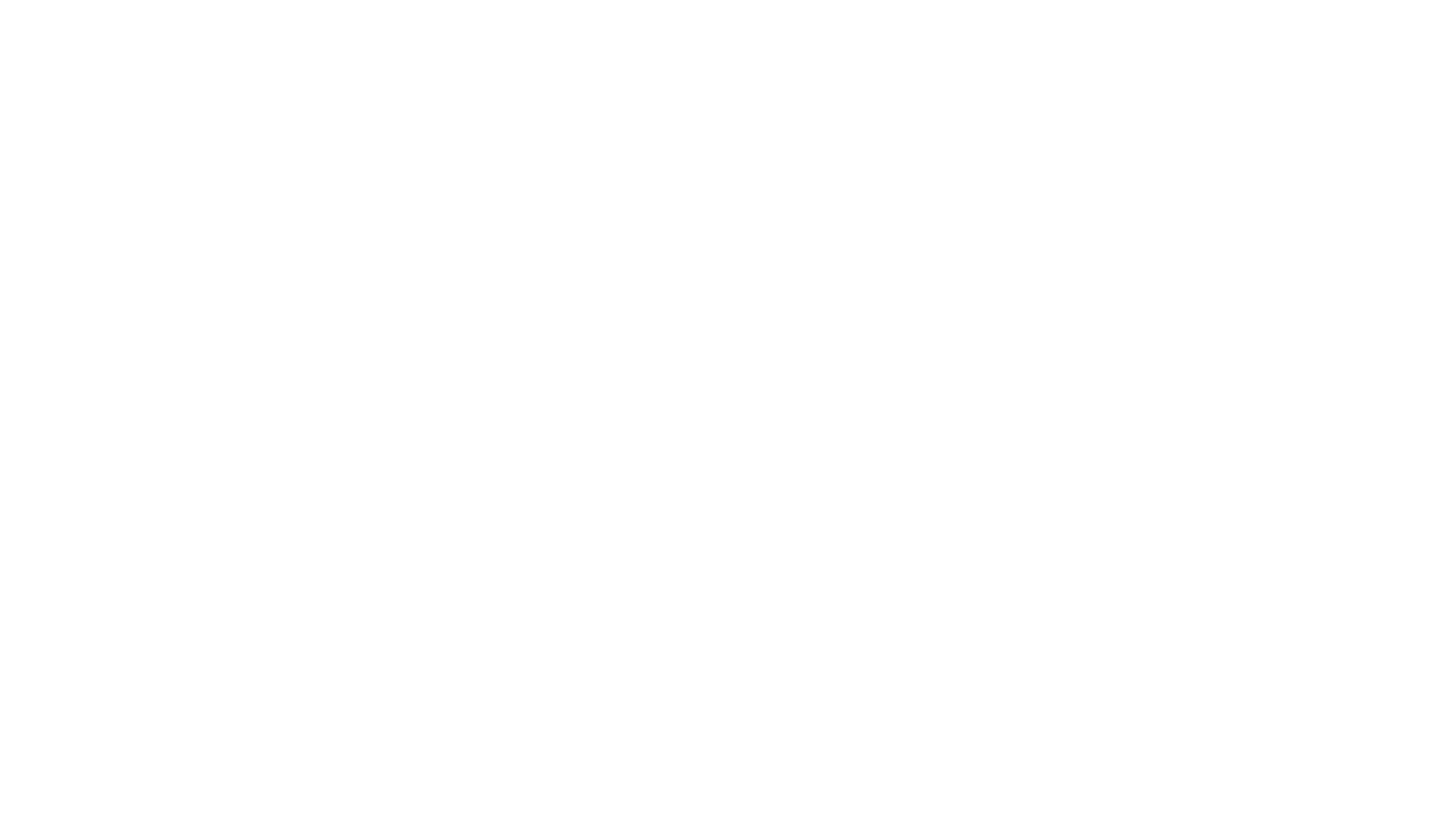
- Отклонения от среднего значения для этих размеров примерно +0,04 мм. Нам известно, что эти элементы обрабатывала фреза диаметром 16.
Доработка
Чтобы дообработать эти элементы, необходимо внести коррекцию на радиус.
- Перейдем в область управления, раздел «Износ».
- Выбрав инструмент 16, добавим в столбец «Дельта» радиус −0,02 мм (половину от отклонения 0,04 мм).
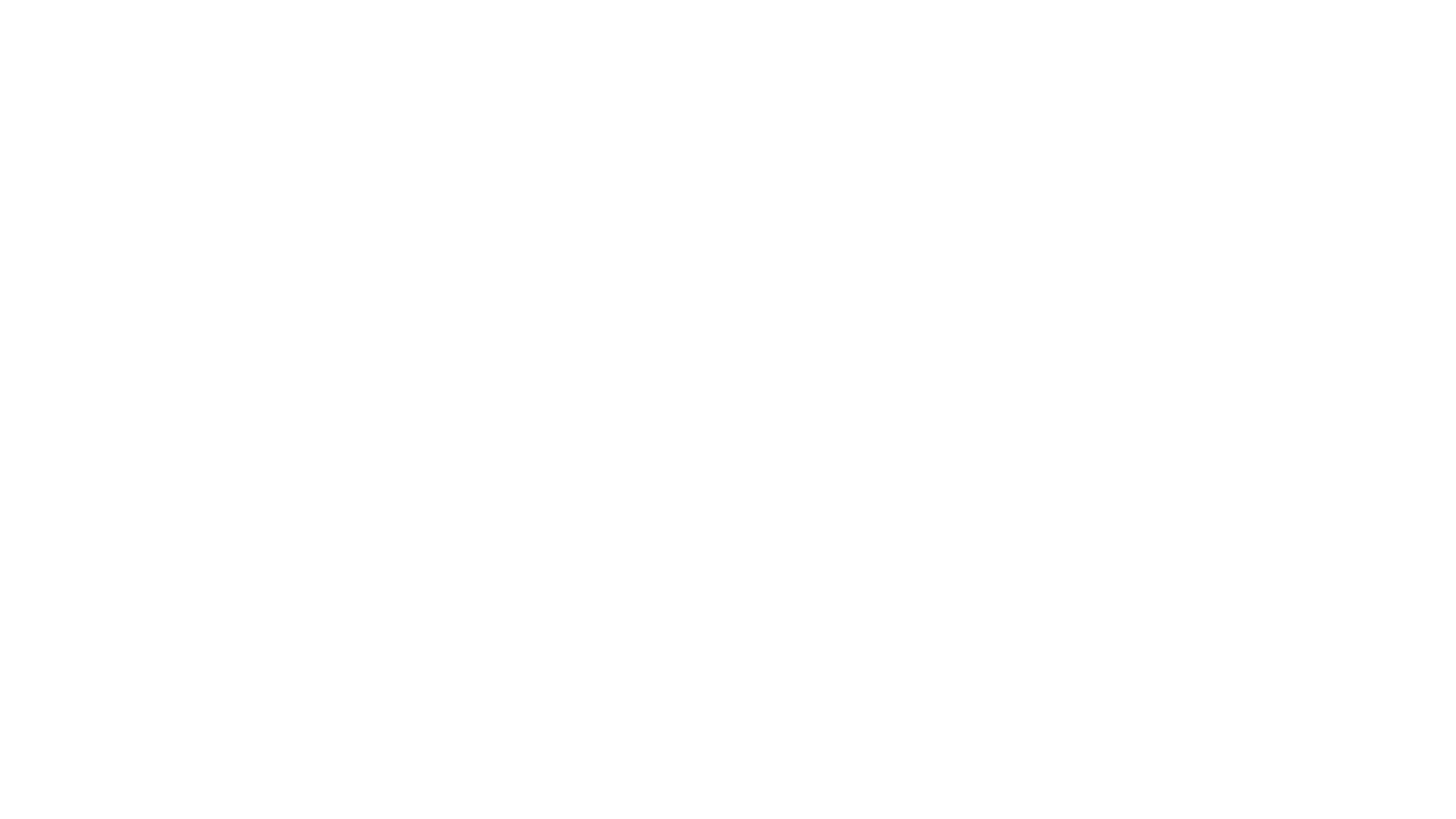
Таким образом, при повторном запуске фреза снимет на 0,02 мм больше материала с каждой стенки.
Измерения. Фреза 6
Перейдем к измерению размеров элементов, которые выполнялись фрезой 6.
Измерения. Фреза 6
Перейдем к измерению размеров элементов, которые выполнялись фрезой 6.
- Измерим отверстие при помощи трехточечного нутромера. Действительный размер меньше среднего значения на 0,04 мм.
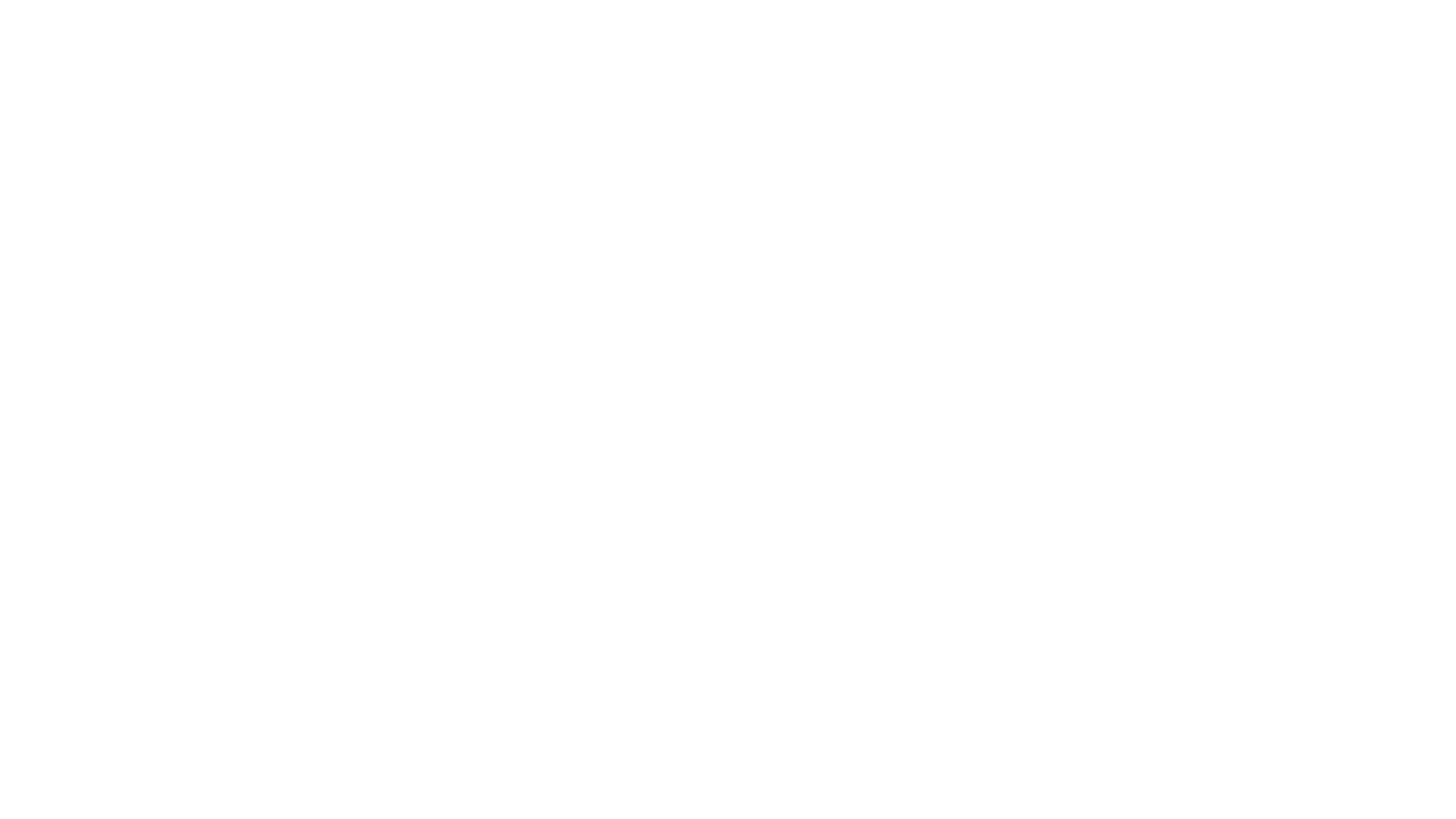
- Размеры кармана 28 и 18 измерять не будем, но проконтролируем концевыми мерами длины. Для этого соберем наборы, соответствующие минимальному и максимальному размерам, и будем использовать как проходной и непроходной калибры. Наборы, соответствующие минимальным размерам, не проходят в пазы. В совокупности с измеренным отверстием это значит, что необходимо снять слой материала.
Доработка
- По аналогии внесем коррекцию на радиус −0,02 мм. Знак минус, т. к. нам необходимо удалить материал.
- Запустим чистовую обработку и по завершении перепроверим каждый размер.
Как и предполагалось, коррекция сработала и все размеры оказались в допусках, а значит, годными.
По аналогии проведем обработку второй стороны детали, контроль и корректировку размеров.
Оптимизация управляющей программы
Когда обработка позади, имеет смысл проанализировать и оптимизировать управляющую программу. Это актуально, когда тип производства от мелкосерийного. Чем крупнее серия, тем важнее становится время обработки, затрачиваемое на одну деталь.
Отходы и подходы
В целом подходы и отходы инструмента подобраны правильно, и изменять их нецелесообразно. В программе они должны быть определены из условий необходимого и достаточного расстояния, т. е. минимальные подходы, отходы и переходы, не создающие столкновений между оснасткой, инструментом и заготовкой. Значит, вспомогательное время сократить не получится.
Частота вращения
Отходы и подходы
В целом подходы и отходы инструмента подобраны правильно, и изменять их нецелесообразно. В программе они должны быть определены из условий необходимого и достаточного расстояния, т. е. минимальные подходы, отходы и переходы, не создающие столкновений между оснасткой, инструментом и заготовкой. Значит, вспомогательное время сократить не получится.
Частота вращения
- При обработке фрезой диаметром 16 мм частота вращения составляла всего 4000 об/мин при подаче 600 мм/мин. Легко рассчитать, что скорость резания составляет около 200 мм/мин, а подача на зуб для трехзубой фрезы — 0,05 мм/зуб. Имеет смысл увеличить скорость резания, увеличив частоту вращения до 8000 об/мин. Это позволит увеличить подачу до 1200 мм/мин без потери качества обрабатываемой поверхности.
- Для того чтобы внести подобные небольшие изменения, не обязательно обращаться к CAM-системе. Достаточно перейти в область управления и, используя функцию «Найти», переместить курсор в начало чистовой операции инструмента 16.
- Находим частоту вращения. Кадр, содержащий S4000 + M3, изменим на S8000. Ниже видим строку с подачей F600, которую меняем на F1200.
Важно
Если вы понимаете, что необходимо более глубокое изменение программы, имеет смысл сделать это в CAM-системе и заново постпроцессировать управляющую программу
Особенно актуально проводить оптимизацию для операций черновой обработки, т. к. зачастую они имеют наиболее продолжительную траекторию и увеличение скорости подачи или глубины и ширины обработки может значительно сократить общее машинное время.
“
Итак, мы завершили обработку детали, окончательно обработали стенки, скорректировав радиус инструмента и добившись годности всех размеров. Мы нашли возможность увеличить режимы резания и исправили их в программе. Давайте повторим пройденное, выполнив несколько заданий.
Дополнительные материалы
Интерактивное задание
Тест
Для закрепления полученных знаний пройдите тест
Стартуем! |
Где находится кнопка «Выполнить» для запуска в автоматическом режиме без редактирования?
Дальше |
Проверить |
Узнать результат |
Какова будет скорость резания при обработке фрезой диаметром 16 мм с частотой вращения 4000 об/мин при подаче 600 мм/мин?
Дальше |
Проверить |
Узнать результат |
Как увеличить скорость резания?
Дальше |
Проверить |
Узнать результат |
К сожалению, вы ответили неправильно на все вопросы
Прочитайте лекцию и посмотрите видео еще раз
Пройти еще раз |
К сожалению, вы ответили неправильно на большинство вопросов
Прочитайте лекцию и посмотрите видео еще раз
Пройти еще раз |
Неплохо!
Но можно лучше. Прочитайте лекцию и посмотрите видео еще раз
Пройти еще раз |
Отлично!
Вы отлично справились. Теперь можете ознакомиться с другими компетенциями
Пройти еще раз |